-3%20big%20pumps-inlet%20(pipes%20close%20to%20me)%20%26%20outlet(direct%20vertical)%2C%201.jpg)
Midland Corrosion Services
Case Study
MIC in Radiators
Building: Large government office building.
Manifestation: Blocking of radiators with sludge and pinhole leaks in the bottom of radiators under sludge with a few years of operation.
Cause: LTHW system contained a large amount of non-barrier plastic pipework which allowed oxygenation of system water. Iron oxide corrosion debris accumulated in bottom of radiators and growth of sulphate reducing bacteria (SRB) under sludge led to microbial influenced corrosion (MIC) and localised pitting.
Solution: System too badly affected for any remediation to be effective. Replacement of failed radiator and monitoring of corrosion inhibitor and biocide treatments
SCC in Stainless Steel Water Jacket
Building: Food Factory
Manifestation: Leaks in stainless steel hot water jacket surrounding pipe delivering chocolate. Due to stress corrosion cracking initiating from corrosion pits in stainless steel.
Cause: Incorrect grade of austenitic stainless steel installed (304 instead of 316) to resist pitting in high chloride water
Solution: RO water used to eliminate chloride from water. Passed through dolomitic limestone filter to reintroduce some hardness to water.
Erosion Corrosion of Brass Valve Seat
Building: Large 4-story office block
Manifestation: Brass control valves to fan coil units ‘letting by’ therefore giving poor temp control and waste of energy in air conditioning system.
Cause: Erosion corrosion with some possible cavitation due to high levels of ammonia in the system as a result of microbial degradation of nitrite/nitrate inhibitor and low pressures at top of the building.
Solution: Replace affected valves and flush out and inhibit the system with a non-nitrite inhibitor. Increase system pressures to prevent the risk of cavitation at top of building.
Widespread Corrosion in LTHW and CHW Systems
​
Building: Large Business Park
Manifestation: Blockage of pipework, failure of boilers and condenser coils
Cause: Insufficient installed expansion capacity and poor maintenance of system pressures leading to large water losses with consequent gross aeration of system water and loss of inhibitors.
Solution: Remedial flushing of pipework where possible but large replacement of pipework and system components necessary. Installation of larger expansion vessels and increase to system pressure. Proper maintenance regime introduced.
Inappropriate Water Treatment​
​
Building: College
Manifestation: Blockage of radiators due to a large amount of alumina debris
Cause: Alkaline corrosion inhibitor used which resulted in corrosion of aluminium boilers and circulation of alumina corrosion product.
Solution: Carry out water treatment analysis and change the inhibitor if necessary. Real-time monitoring of boiler condition suggested.
SCC of Brass Fitting Under Insulation​
​
Building: Office chilled water system
Manifestation: Leakage of brass valves under thermal insulation
Cause: Poorly fitted phenolic foam insulation allowing condensation on pipe. High applied torque to fittings coupled with leaching of ammonia resulting in stress corrosion cracking of fitting from outside.
Solution: Replacement of affected valves. Repair of insulation to prevent condensation on pipework
Pitting Corrosion of Cu Pipe​
​
Building: Domestic cold water system
Manifestation: Pinhole leaks of copper pipework
Cause: Water stagnation occurred in the cold water system allowing Type 1 pitting to develop on the Cu pipework.
Solution: Regularly flush the pipework to introduce fresh aerated water allowing for the build-up of a stable and protective malachite protective film on the pipe bore.



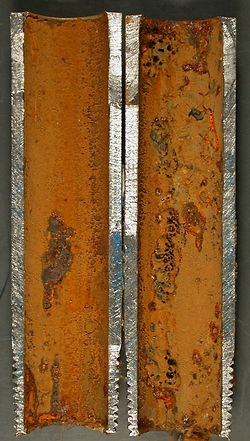

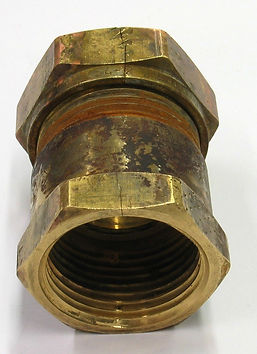

Blockage of Plate Heat Exchanger​
​
Building: Water cooling system
Manifestation: Blockage of PHE with limited flow of water
Cause: Accumulation of calcium carbonate limescale and corrosion product debris blocking the flow of HE.
Solution: Carry out water sampling analysis; de-scaling and pressure test introduced.

Corrosion of Galvanised Rotor Blades​
​
Building: Wastewater Treatment Plant
Manifestation: Failures of hot dip galvanised blades attached to rotors used to aerate and move effluent in an oxidation ditch. The blades were corroded and fractured resulting in the failure of the rotor assembly.
Cause: Hot dip galvanising and the underlying carbon steel was not suitable for the exposure conditions of this specific wastewater.
Solution: In conjunction with the aerator designer to replace the rotor assembly with a dual coating system (e.g. epoxy coated galvanised steel) or using higher grade steel such as 304L or 316L stainless steel.

Compatibility Testing of Solvent​
​
Reason: For regulatory reasons the client had to replace the current solvent. A number of replacement solvents were tested to establish the one least corrosive to the various material used in the pipework, storage tanks and vessels.
Approach: MCS reviewed the solvents’ MSDS, condition of use as well as materials in the system to establish suitable test conditions which simulate the worst exposure environment in the laboratory.
Testing: Immersion testing was carried out at 80°C with coupons being exposed to both the liquid and vapour phase. This enabled the interface between the two phases to be studied. The interface was judged to be most at risk from corrosion.
Evaluation: The coupons were removed from the test solution at intervals and evaluated for weight loss in accordance with ASTM G1 and the type of corrosion attack using microscopy.
